Chemical Handling and Manufacturing Safety
Safety in the chemical industry is essential — with workers regularly handling hazardous chemicals, protection is a must. Personal Protective Equipment (PPE) reduces the safety risks of hazards that cause injuries and illnesses in the workplace. Any industry working with hazardous chemicals is open to accidents — proper safety procedures and equipment help create safer work environments.
For quality chemical plant safety, PPE is vital protection for anyone working with hazardous chemicals. Learn more about PPE and the safe handling of chemicals with this guide.
Industries That Handle Chemicals
Almost every industry handles hazardous chemicals in some capacity. With so many chemicals involved in different sectors, chemical safety risks are everywhere. Hazards in the chemical industry are avoidable partly with the help of PPE.
In 2019, Large Quantity Generators (LQGs) in the United States produced over 34.9 million tons of hazardous waste. To be an LQG, there must be 1,000 kilograms or more of hazardous waste or over one kilogram of acutely hazardous waste produced in a month. The four primary industries that produce the highest amounts of hazardous waste in the United States are:
- Metal fabrication
- Primary metal production
- Petroleum processing
- Chemical manufacturing
The large output of hazardous waste by these companies means its vital workers are protected at all times from the chemicals they’re working with. In industries with hazardous chemical handling, chemical exposure comes in four forms — solid, liquid, gases and vapors or dust. Proper PPE is necessary to block the harmful effects of chemical exposure and ensure workers can perform their jobs safely and effectively.
Why PPE Is Important for Handling and Manufacturing Chemicals
PPE is essential to worker safety. Without PPE, workers are exposed to harmful chemicals and processes that can negatively impact their health. Protective gear is a worker’s first line of defense and an essential part of working with chemicals safely.
With the proper protective equipment, workplaces will function better. Employees exposed to hazardous chemicals without protection will have fewer accidents and injury rates. Healthcare workers without PPE have higher rates of illness than workers with adequate PPE. The more workers that become sick or injured on the job, the more shortages and stalls a workplace will experience. Protecting workers protects output and allows your facility to run at its best.
PPE protects against immediate chemical-handling dangers and defends workers from long-term safety effects. Long-term exposure to hazardous chemicals can lead to severe health conditions. Mesothelioma, skin issues, organ damage, reproductive problems and more can all occur due to extended chemical exposure. PPE will protect workers from immediate dangers and issues down the road.
Having proper PPE also provides workers with an improved working environment. Without PPE, jobs can become more complicated, dangerous and uncomfortable to complete daily. For example, industrial worker PPE prevents serious injury from equipment and chemicals, helping them work with hazardous equipment more efficiently. Having the right equipment can help workers feel safer and reduce the strain of their job, making workplaces more comfortable and efficient.
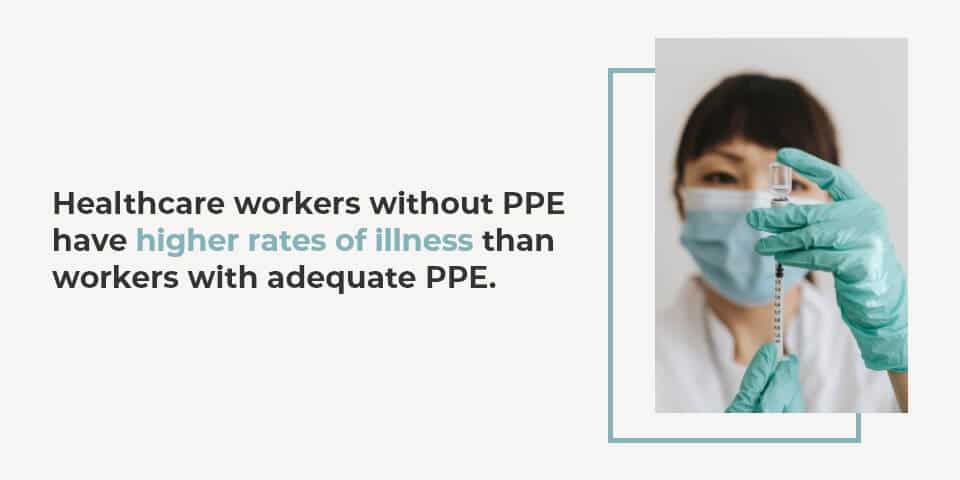
Types of PPE for Handling and Manufacturing Chemicals
To protect workers and ensure the safe handling of chemicals, you need the right PPE for the job. Groups working with hazardous chemicals must follow Occupational Safety and Health Administration (OSHA) standards to create a stable and secure environment, which means following proper procedures and supplying the right PPE. PPE should meet OSHA regulations to ensure workers are adequately protected from the chemicals they’re working with.
Let’s look at the four levels of PPE and what each includes:
Level A
Level A protection is the highest level. Workers need Level A PPE when their job has the highest possible level of hazardous exposure and therefore need the most eye, skin and respiratory protection. Level A PPE can include:
- Inner and outer chemical-resistant gloves
- Disposable protective gloves, boots and suit
- Fully encapsulated vapor- and chemical-protective suit
- Chemical-resistant, steel-toed footwear
- Positive pressure supplied air respirator with escape self-contained breathing apparatus (SCBA) or full-facepiece, positive pressure SCBA
Level B
If respiratory dangers are at the highest level, but less skin and eye protection are needed, you should have Level B PPE. PPE for these sites would be:
- Face shields
- Hooded chemical-resistant clothing
- Inner and outer chemical-resistant gloves
- Coveralls
- Outer, steel-toed chemical-resistant boots
- Positive pressure supplied air respirator with escape SCBA or full-facepiece, positive pressure SCBA
Level C
Level C protection is needed for conditions with known airborne substances and their concentrations. Air-purifying respirators are essential, but skin and eye protection aren’t required except for emergencies. Level C PPE includes:
- Hard hat
- Inner and outer chemical-resistant gloves
- Disposable chemical-resistant outer boots
- Full-face purifying air respirators
Level D
Level D is the lowest level of protection. If work conditions prevent immersion, splashes or the potential for incidental contact or inhalation of hazardous chemicals, then you only need Level D PPE. This protection could include:
- Face shields
- Safety glasses
- Steel-toed, chemical-resistant boots
- Gloves
- Coveralls
Tips for Handling and Manufacturing Chemicals Safely
The key to a safe workplace is proper procedures and protection. With excellent training and safety measures, you can reduce the health risks for your workers and maintain a healthy and productive environment. Here are some tips for safer, better handling of chemicals in the workplace:
- Understand the chemicals: The first step to secure chemical handling is understanding the chemicals you’re working with. Chemical suppliers will provide you with a Safety Data Sheet (SDS) with all the information you need. Once you know what you’re dealing with, you can get the right PPE, create handling procedures, store the chemical and educate your staff.
- Provide the right PPE: The PPE you need depends on the chemicals you’re handling. The SDS will tell you what PPE is necessary — provide it to your workers to ensure they have safe conditions to work in.
- Safely store chemicals: Chemicals need the proper storage — some chemicals can have dangerous reactions with others, leading to fires, toxic gas clouds and explosions. The SDS will help you store the chemicals correctly, keeping your workers safe and your facility government-compliant.
- Ensure good training: Safe storage and PPE isn’t enough — your staff should have thorough training to ensure they understand how to handle chemicals safely. This includes staff working with the chemicals regularly and any staff visiting the site or working near it. Quality, thorough training helps protect everyone on your team and keeps accidents from happening.
Choose SUNLINE Supply for Your PPE Needs
You want to ensure your workplace is a safe, healthy place to work. High-quality PPE is essential for any company working with potentially hazardous materials. If you want safe, regulation-compliant PPE, show our wholesale safety products and keep your workplace protected. Contact us online with any questions and get started on your order today!
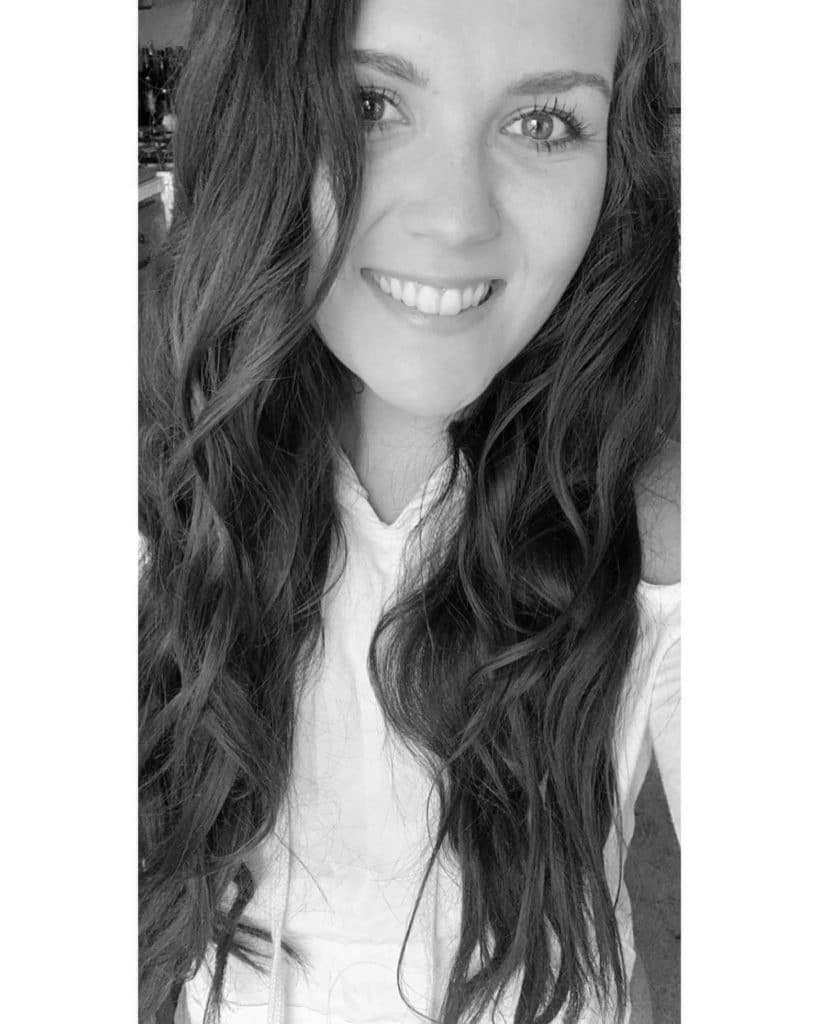
🙂