Elements of a Respiratory Protection Program
Workplaces, including manufacturing, biochemical production, construction, research and other industries, may expose workers to airborne contaminants. Having the right personal protective equipment (PPE) and a respiratory protection program can help keep your team safe.
When Is a Respiratory Protection Program Needed?
The Occupational Safety and Health Administration (OSHA) mandates employers to implement a written respiratory protection program if:
- Workers need respirators.
- Contaminant levels reach beyond permissible amounts.
Determining whether you need a respiratory protection program begins with evaluating workplace contaminants and the current permissible exposure limits. You also need to consult local, federal and state requirements to determine whether you need a program. If your workplace already requires respirator use, you do need a respiratory protection program.
What Is Required in a Respiratory Protection Program?
Respiratory protection program requirements depend on your location, local and state rules and the potential contaminants at your site. An industrial hygienist can evaluate airborne hazards and possible requirements you may need. In general, most programs will require:
- An understanding of policies and procedures: OSHA outlines the rules and policies for protection programs for airborne contaminants.
- A written plan: You will need a written, formal plan which is overseen by a qualified program administrator.
- Exposure assessments: A professional experienced in exposure assessment methods must evaluate the workplace to determine what airborne hazards exist and whether the contaminants exceed acceptable levels. Any time there is a seasonal change, your organization purchases new equipment or any possible change in contaminants, you will need a new assessment.
- Respirator selection: All respirators need to be a brand and model approved by the National Institute for Occupational Safety and Health (NIOSH). They must also have the assigned protection factor (APF) suitable for the contamination level. This APF can be anywhere from 10 to 10,000.
- Medical evaluation and fit testing: Workers need to complete a medical questionnaire and have it approved by a licensed health care professional to determine whether workers can wear the respirator. If a worker is approved, they must undergo fit testing to ensure the respirator offers good protection.
- Maintenance: Workers must learn proper safety processes once a year. Any respirators used need to be regularly maintained, following the manufacturer’s guidelines. Employers must evaluate the respiratory protection program regularly and update it if needed.
Buy Masks in Bulk at SUNLINE Supply
SUNLINE Supply is your partner in PPE and workplace supplies. We are a company with high-rated masks and PPE products from vendors. SUNLINE Supply makes it easy to buy in bulk or small orders. Buy masks in bulk today from SUNLINE Supply for your business program.
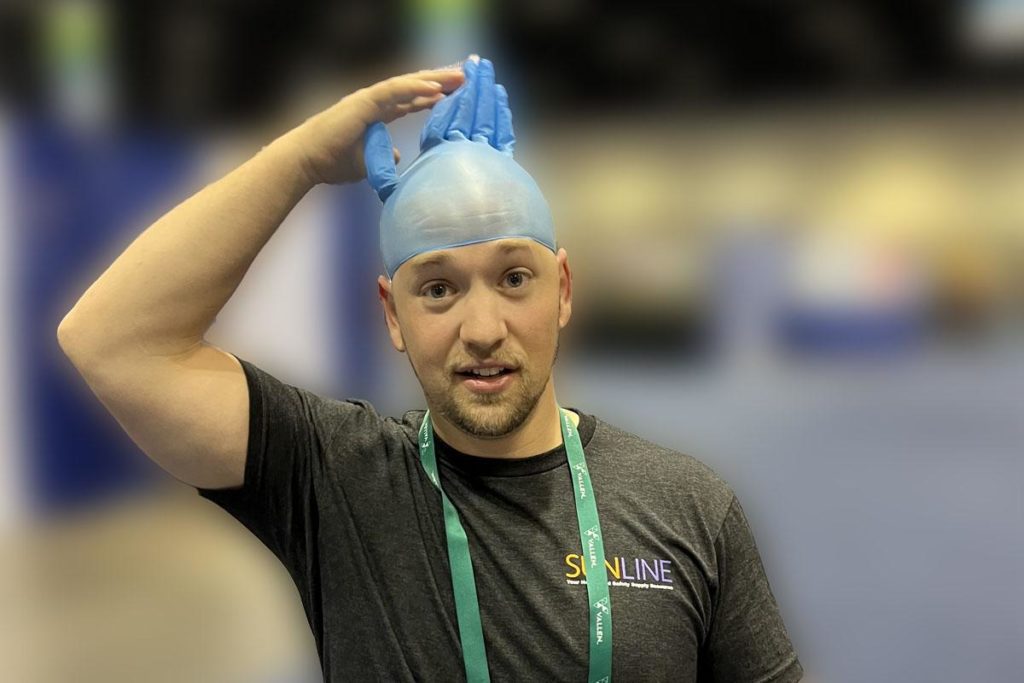